All my products and services are free.
All my costs are met by donations I receive from my users.
If you enjoy using any of my products, please donate to support me.
My bare hosting costs are currently not met so please consider becoming a contibuting member by either clicking this text or the Patreon link on the right.
|
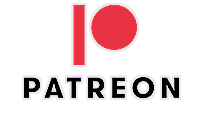
|
If neither of those of work for you, you can donate any amount by clicking here. |
Recommended Posts
Join the conversation
You can post now and register later. If you have an account, sign in now to post with your account.